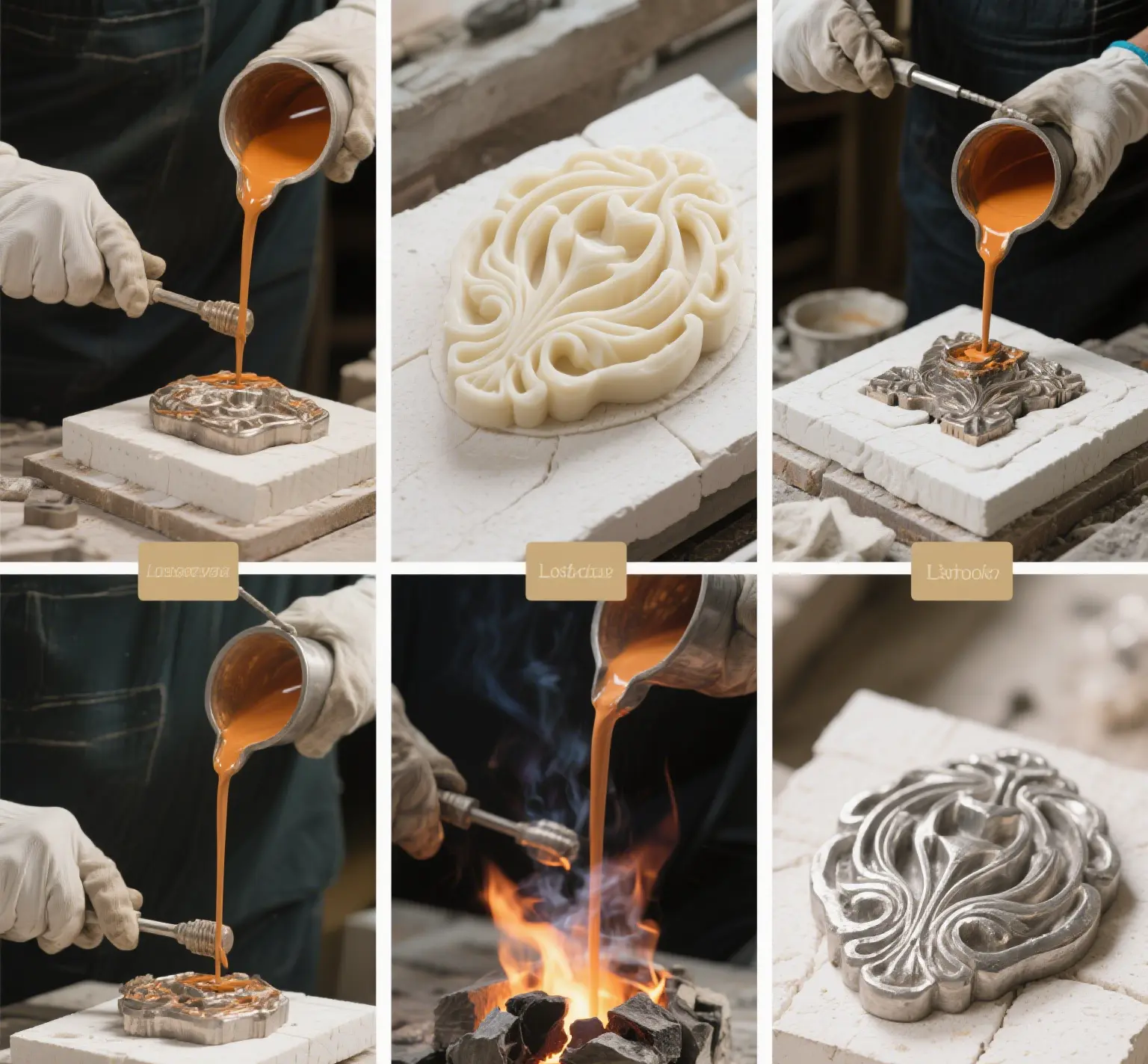
Lost Wax Casting: Process, Techniques, and Industry Applications
Key Takeaways
- Lost wax casting has been used for thousands of years to produce intricately detailed metal objects. It’s a technique that’s employed by artists and industries all over the United States.
- This technique allows for more detailed designs. Its ability to work with an extensive array of metals gives it terrific versatility for everything from custom jewelry to sculptures to precision parts.
- Each process requires a delicate touch and precision tools. From modeling in wax to pouring the molten metal, working with quality materials will always yield the highest quality results.
- Advances in technology, such as new digital design processes and 3D printing, have improved the efficiency and precision of traditional lost wax process casting.
- Quality control, careful temperature management, and appropriate material selection play a critical role in minimizing defects and creating high-quality castings.
- By following safety guidelines and using eco-friendly practices, both the maker and the environment can be safeguarded during casting projects.
The lost wax process casting is an investment casting process, a metal casting technique that begins with the production of a wax model. Second, a mold is formed around the model, and then we melt the wax out and pour in molten metal. This incredible technique was born from the ancient art and industry.
You can see its uses in jewelry, sculptures, dental work, and machinery parts right here in the United States. It’s popular among foundries and artists for its ability to render crisp detail. It allows for intricate shapes that are hard or impossible to produce using other techniques.
While every shop is different, most utilize metals such as bronze, gold, and stainless steel. Lost wax casting is an incredible process that facilitates everything from museum quality, one-off art pieces to larger runs for the manufacturing industry. The following sections walk through the major steps and contemporary applications in the U.S.
What is Lost Wax Casting?
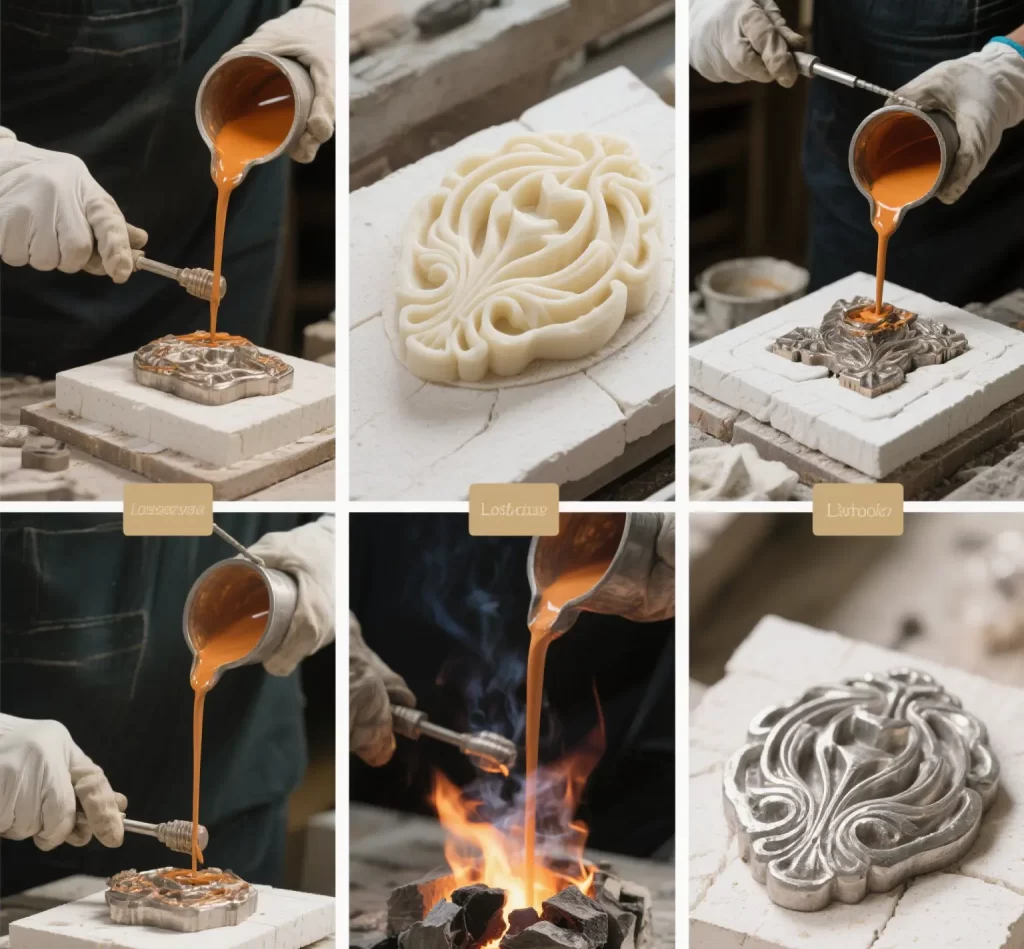
Lost wax casting is a technique used to create detailed metal objects. This model is then encased with a heat resistant material, known as a refractory. Once the wax has melted out, it creates a hollow void. Molten metal poured into this cavity assumes the precise shape of the original wax.
This method has really stood the test of time, with roots going back at least 5,000 years. It’s appreciated not just for its historic use, but for its ongoing practice today and in contemporary making. Nowadays, you can find lost wax casting in industries as diverse as fine art, jewelry, and manufacturing.
The process is celebrated for its unique quality of reproducing intricate, detailed designs in metal. Its depth and versatility quickly established it as the medium of choice for pieces requiring a high degree of artistry.
1. Defining This Timeless Technique
Lost wax casting begins with a wax model. This model is a perfect representation of the resultant work. After the wax is complete, it’s coated in a shell of hard, heat-resistant material.
When the wax is melted out, it creates a mold that’s ready for casting with metal. The result is a beautiful metal object that literally follows the wax design, right to the last engraving. The journey this process has been on is long and far-reaching, from the earliest city-states of Mesopotamia to today’s studios and shops.
Unlike sand casting, which almost universally lacks crisp detail, lost wax casting can render fine lines, textures, and shapes. This level of detail is essential to both artistic expression and functional necessity. Every single step in the process needs to be executed with precision, as even the slightest misstep will be apparent in the final product.
2. A Quick Look Back: History
The oldest surviving examples of lost wax casting come from the 3rd millennium BCE. Bronze statues and implements cast using this method have been discovered in Mesopotamia, the Indus Valley, and sub-Saharan Africa. These discoveries are a testament to the invaluable process that was revered around the world.
Lost wax casting continued to spread, appearing in ancient Greece, ancient China, ancient Egypt, and pre-Columbian South America. Greek bronze statues, Benin bronzes from Nigeria, and early Buddhist figures from Asia exhibit characteristics of this process.
Artists and makers continued to use lost wax casting throughout history because it provided them the ability to create intricate, long-lasting pieces. Many artifacts like the dancing girl of Mohenjo-daro and the Benin plaques intrigue us because of their stunning artistry and detail. It’s no wonder that their enduring beauty continues to captivate today.
3. Why It Still Matters Today
Today, it is a link between ancient craft and contemporary demand. Artists have found it to be an ideal method to create highly intricate sculptures that simply cannot be produced by any other method. Jewelry makers use it for fine rings, pendants, and custom pieces that require aesthetic value and durability.
Even in industry, the process is used to produce detailed machine parts that need to fit very close tolerances. The process lends itself beautifully to stainless steel, brass and silver—metals commonly used in custom jewelry. Chinese companies like HonHo Jewelry rely on lost wax casting to create waterproof, non-tarnish jewelry that they sell all over the world.
Advances in wax types, casting technology, and mold making have completely changed the process. Today, it’s able to produce much more intricate and grander scale works with ease. The introduction of 3D printing for creating wax models has opened the door even further, greatly accelerating the process and enhancing repeatability.
4. The Basic Steps Explained Simply
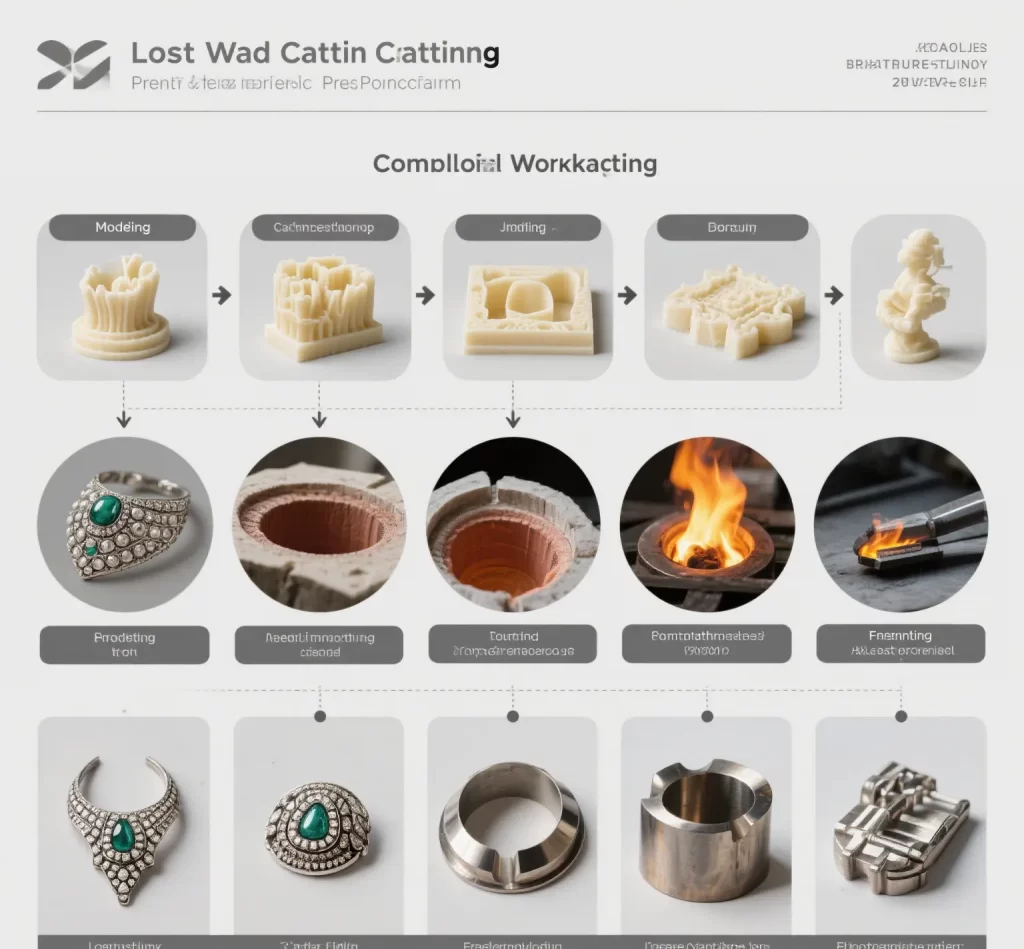
- Modeling: Make a wax model of the item.
- Investing: Coat the model with a ceramic or plaster shell.
- Burnout: Heat the shell to melt out the wax, leaving a cavity.
- Casting: Pour molten metal into the empty shell.
- Breakout: Remove the shell to reveal the metal piece.
- Finishing: Clean and polish the final item.
These steps are usually done in this order, and if done properly, the result will be a high-quality casting. Each requires a unique set of tools—such as carving knives for wax, kilns for burnout, and personal protective equipment for casting.
The entire endeavor is rooted in precision and care at each step of the process.
5. Creating Your Wax Model
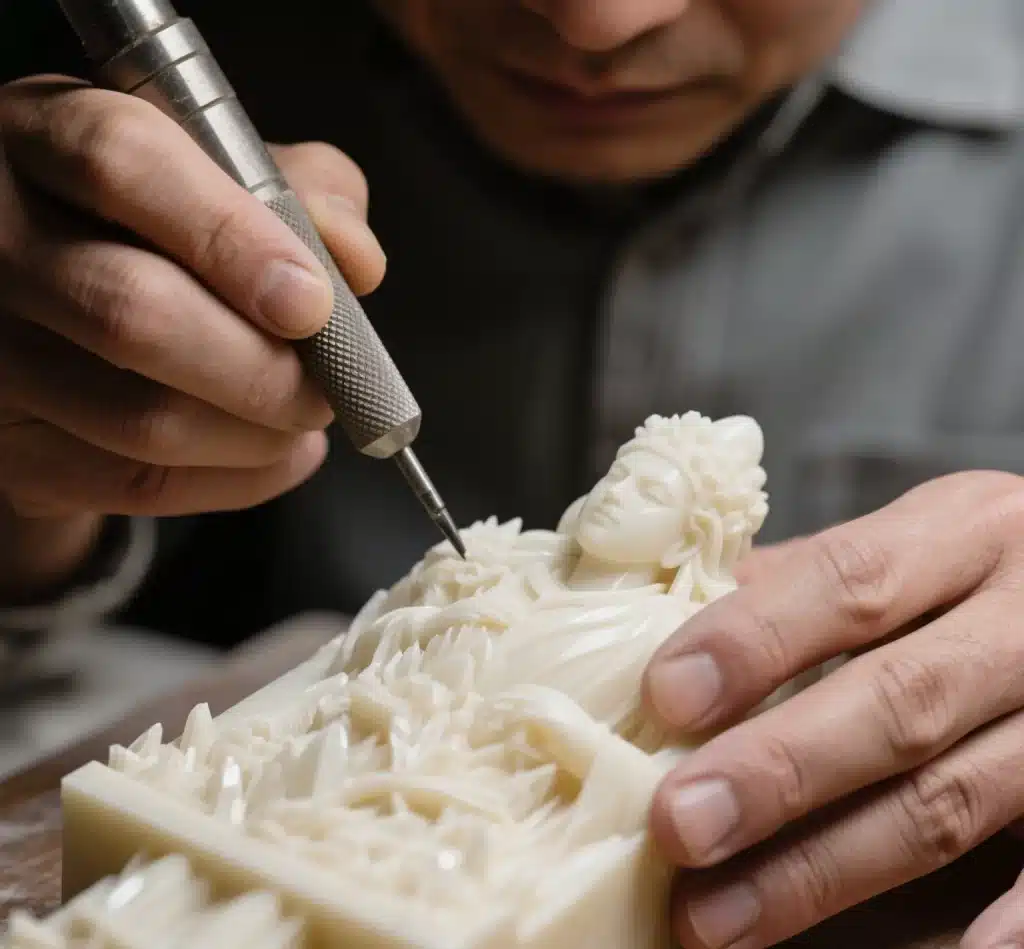
Your wax model is the foundation for all that comes after. Many makers prefer to work with microcrystalline wax, which is more yellow in color, softer, stickier and easier to manipulate. The model can be carved out by hand, molded or even printed with 3D technology.
Specialized fine tools allow artists to create texture, furrow lines, and small details into the model. It’s important that the wax model be perfect, as any imperfection will be evident in the finished product. Before proceeding, artists check the wax model for final touches, smoothing out any bumpy areas or imperfections.
6. Building the Ceramic Shell
Once the wax is injected and cooled, the model is dipped or otherwise coated in a slurry of ceramic or plaster to build up a hard shell. This shell needs to be heat proof and not break when the metal is poured inside.
Producers frequently dip using multiple thin layers to construct a fine, durable finish. The shell has to dry completely between layers. The ideal is a mold that can withstand the heat of burnout and the shock of molten metal.
7. Melting Out the Wax
After the shell hardens, it gets loaded into a kiln or furnace. The heat melts out the wax, which runs out leaving an empty cavity for the metal. This step requires careful management of temperature to prevent the shell from cracking or distorting.
All evidence of wax needs to be removed, or else the casting will crack. Health & Safety Makers wear heat-resistant gloves and eye protection, as there are dangers associated with high temperatures and molten wax.
8. Pouring the Molten Metal
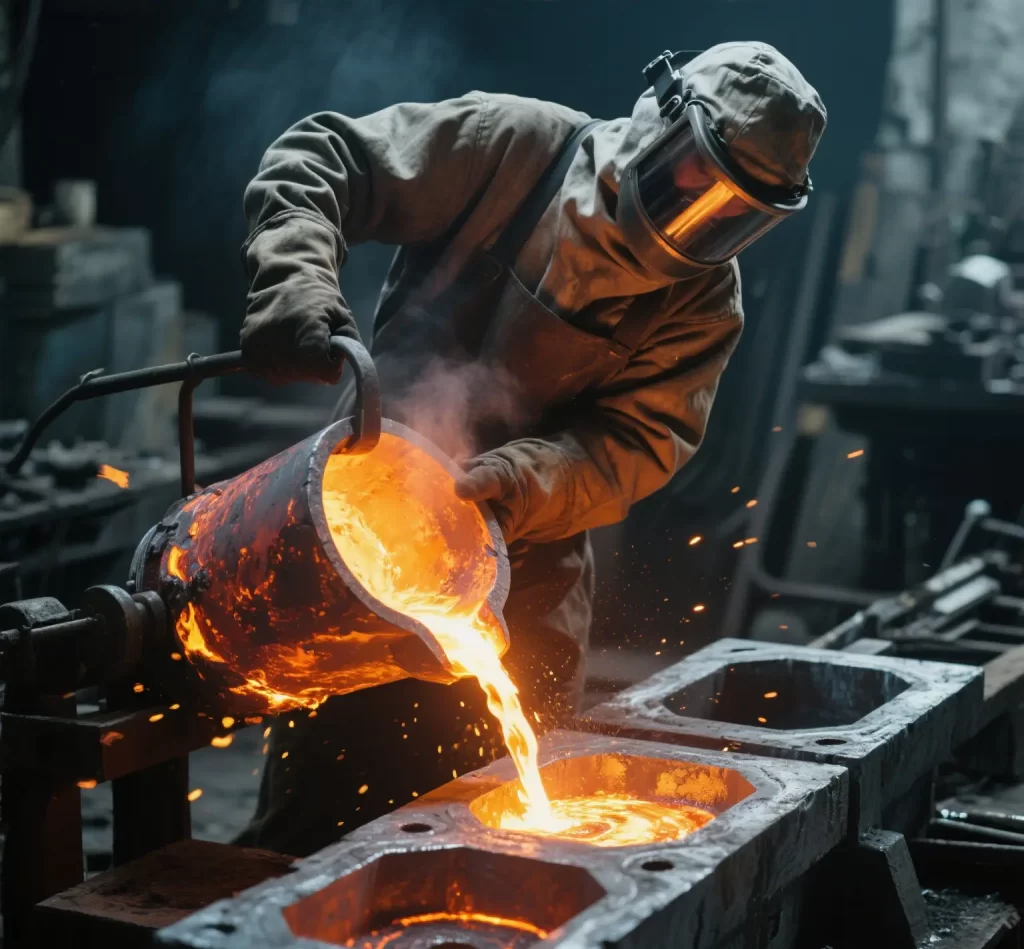
Then, the shell is heated once more before molten metal—typically bronze, brass, silver or steel—is poured into the cavity. Maintaining the metal’s temperature during this process is critical to ensure it fills all the contours and intricacies of the mold.
The shell needs to be in an upright and stable position to prevent spills and defects. Pouring the metal too quickly or not quickly enough will create bubbles or gaps.
9. Breaking Away the Mold
Once the metal has cooled and hardened, the shell is broken away. Depending on a maker’s preference, hammers, chisels, or even high-pressure water jets can be used to shatter the shell.
This step requires a great deal of patience, as being hasty may chip or shatter the new metal casting. Once freed, the piece is inspected for cracks, bubbles or other absences of detail.
10. Finishing Your Metal Piece
Your cast piece will probably still have a few jagged edges or bits of shell attached. Metal files, sandpaper, and polishing wheels are used to even out and shine the surface of the cast piece.
Artists and artisans search for places to repair and patch. Some pieces receive a coating—such as lacquer or wax—to protect from wear and tarnishing. These steps really transform the color, shine and fine detail that lost wax casting is famous for.
Essential Tools and Materials
Whether in the studio or during the wax casting technique, each stage of jewellery making relies on the right tools and materials to achieve clean, repeatable results. The essentials remain pretty constant, but there are some decisions that can vary depending on your individual project or studio. Here’s how these essential tools and materials inform the wax casting process steps.
Choosing the Right Wax Type
Wax is available in a wide variety of forms—soft, hard, sticky or even specialty blends designed specifically for carving or injecting. If you’re creating large or simple shapes, softer waxes are ideal, but if you want to maintain a sharper edge for detail, harder types will retain sharper edges.
Specialty waxes are used to hold designs sharp for jewelry work and fine line art. They further reduce the chances of distortion while handling. Think about your end goal: for a sturdy ring, a medium-hard wax might be best; for an ornate pendant, a high-detail carving wax saves headaches.
Never assume, always verify the melt point, as a low-temp wax can lose its shape in handling or burnout.
Investment Mixes: What Works Best
Investment materials, such as Kerr Satin Cast 20 or Ultra-Vest, create the mold around your wax. A well-made mix provides a fine texture and the ability to resist thermal shock. Plaster and silica blends are very common, but the magic is in the mixing.
Accurate ratios and bubble-free mixing (with a vacuum or pressure pot) prevent weak areas or surface imperfections. Many repair shops have switched to citric acid or vinegar for these processes, which are safer and more environmentally friendly.
Selecting Your Metal Alloy
Alloy selection impacts the aesthetic and longevity of your work. Silver and gold are the most popular for jewelry, each requiring a different melting temp and hardness. Bronze or brass are preferred metals for sculpture, providing both strength and rich color.
Always factor in the final use: softer metals polish up faster but can scratch, while harder metals need more work but hold up longer.
Key Equipment You Will Need
- Wax modeling tools and carving knives
- Investment flask and mixing bowls
- Kiln or burnout oven (5–12 hour cycles)
- Torch (often a #3 tip), crucible, stirring rod (preheated)
- Vacuum or pressure pot
- Gloves and safety gear
- Flux for prepping crucibles
- Pickle solutions (citric acid, vinegar, sparex)
Each tool has a defined purpose—modeling shapes, creating molds, pouring metal, or finishing. Quality equipment reduces the chances of injury, increases worker safety, and ensures consistent results.
Specialized tools, such as vacuum casters, advance your craft for intricate work.
Modern Tech Meets Old Ways
The ancient lost wax process, dating back more than 6,000 years, has undergone a renaissance in modern workshops. Now artists and makers are merging these new digital opportunities with old-world casting methods. This powerful combination opens up incredible new possibilities to manipulate materials such as metal and glass.
Digital design, 3D printing, and advanced materials are transforming how we model, mold, and pour. Much of the substance of the process is still the same. This approach connects the past with the present. It allows artisans to shift towards more intricate work that can stand up to modern pressures.
3D Printing Your Wax Patterns
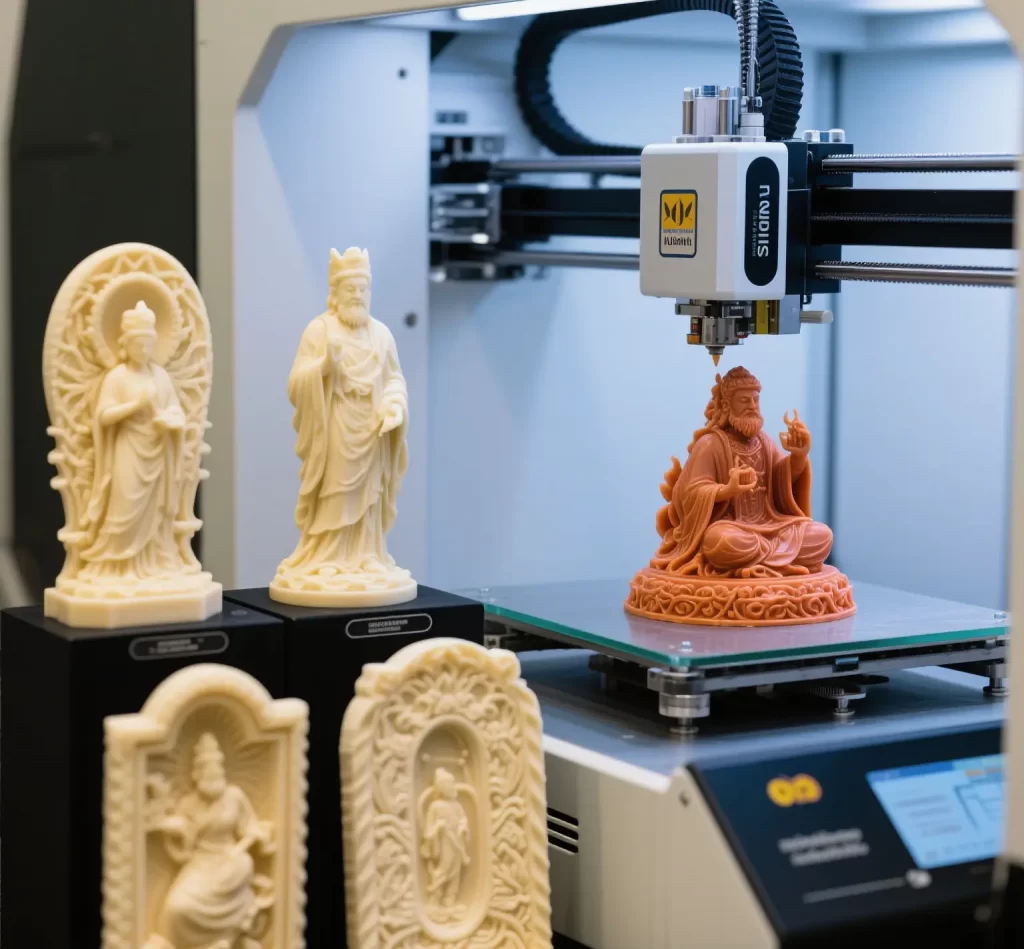
Today, 3D printing allows shops to produce those wax replicas that are precise, right on the money in detail and shape. Casting patterns go from digital file to solid pattern in a few hours, not days. This design process allows artists to prototype, modify, and reprint their creations in rapid succession.
Rapid prototyping is a tool that benefits massive manufacturers and independent artists alike. Jewelry makers, like HonHo Jewelry in China, use 3D-printed wax models for custom, waterproof, and non-tarnish pieces made from stainless steel, brass, or 925 silver. Thanks to this new production tech, it’s less challenging to produce unique styles or entire collections with minimal excess.
Digital Design in Casting
Utilizing CAD software, artists now have the tools and power to create shapes and patterns that are impossible to achieve through hand work. Intricate designs, including cast glass sculptures, begin life as virtual 3D drawings.
These computer files control the operations of 3D printers or CNC machines and remove much of the guesswork from the mold-making stage. With digital design comes fewer mistakes, more thoughtful preparation, and a quicker journey from concept to completed casting.
Combining Speed and Precision
Modern technology makes each step more rapid. Molds created with higher quality materials such as polystyrene foam or fiberglass retain detail and stand the test of time. Makers in aerospace, art, and medical industries depend on lost wax casting.
That’s because this technique provides high precision, tight tolerances and quick turnarounds. Other industry folks lament the loss of traditional craftsmanship. To those who have caught the bug, technology is seen as a way to help keep the craft flourishing and exciting.
Why Choose Lost Wax Casting?
Lost wax casting stands out as a time-tested method for shaping metal objects with a level of precision that many other casting techniques cannot reach. This technique has its origins in some of the great ancient civilizations, including the Indus Valley and Egypt.
Today, it’s still a favorite because of its dependability and adaptability in producing quality parts across many industries.
Unmatched Detail and Complexity
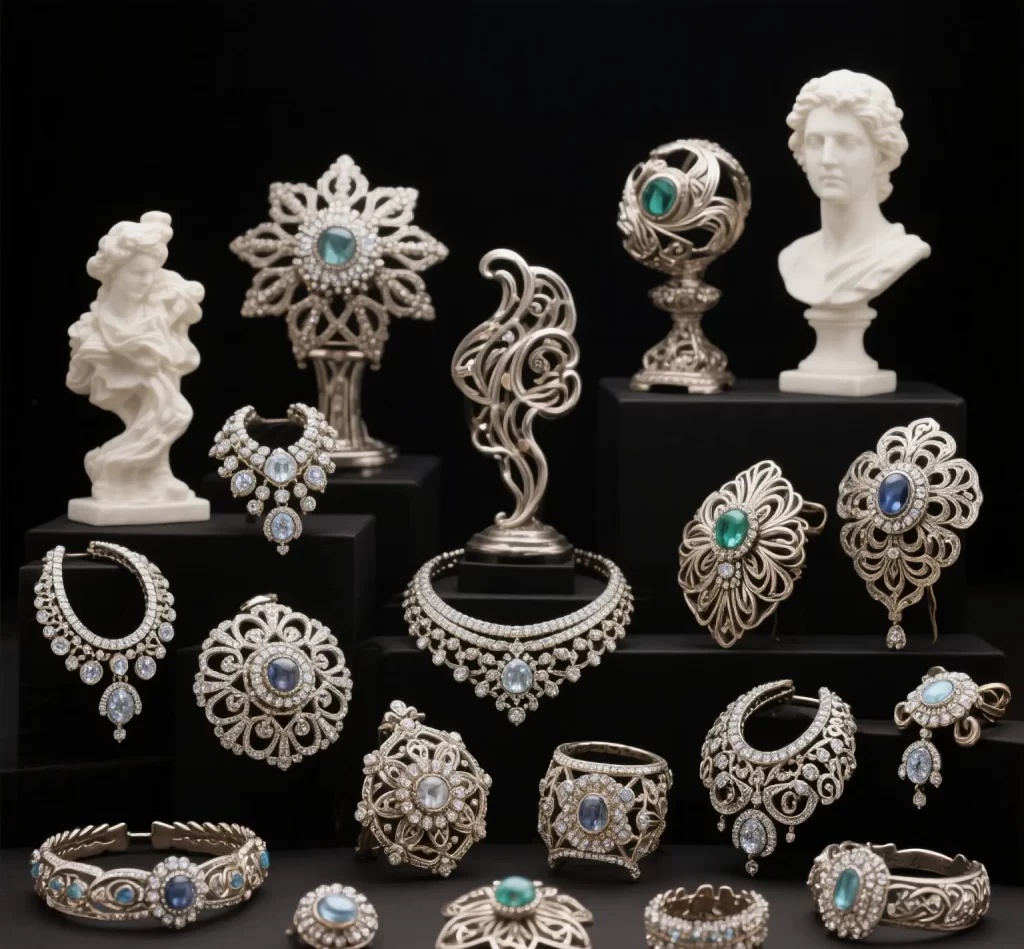
The lost wax process is renowned for creating beautiful surface finishes. This unique method gives artists and artisans the ability to cast an exacting reproduction of their original model.
This allows for hollow castings to be produced using this technique which is ideal for creating more intricate shapes that are lightweight. Jewelers often use lost wax casting to create ornate rings, pendants, and bracelets that need crisp lines and deep textures.
Sculptors in the art world would not be able to achieve high levels of detail like we see in bronze statues without this technique. They lovingly preserve each wrinkle in cloth and crease in countenance.
Always factor in the final use: softer metalsThe process allows for extraordinary detail and organic shapes that other casting processes simply can’t reproduce.
Versatility Across Different Metals
Lost wax casting can be used with many metals — from bronze and copper to gold, silver, and modern alloys. This broad range allows it to accommodate both decorative fine art and functional industrial parts.
For example, the jewelry industry values lost wax casting for gold and silver pieces, while some manufacturers use it for making precise machine components. HonHo Jewelry, your China-based manufacturer, is strong in stainless steel, brass and 925 silver.
This means that they offer waterproof with no tarnish alternatives.
Great for Unique, Custom Pieces
This method is considered the best choice for custom designs. An artist can sculpt, mold, or 3D print a wax pattern, then use it to cast one piece or a short production run.
Signet rings or unique pendants for custom jewelry as well as sculpture prototypes are commonly produced using this method. The almost limitless creative freedom is one of the main attractions of this process for designers and artisans alike.
Relatively Low Tooling Costs
For small production runs or one-of-a-kind pieces, lost wax casting allows you to stay within your budget. This is because you don’t require large, expensive molds in your tooling inventory from the start.
This relatively low barrier to entry allows hobbyists, small studios, and independent artists to produce intricate work on a limited budget. Many craft jewelers and small studios use lost wax casting to produce short runs of unique pieces at a manageable cost.
Understanding the Limitations
Though famed for its miniscule detail and versatility, the wax casting technique has some obvious restrictions. Understanding these challenges helps you better prepare for jewellery making, budget accordingly, and achieve successful outcomes in producing intricate wax cast pieces and metal objects.
It Takes Time and Patience
Each lost wax casting commission requires a significant amount of time. Producing the wax model, particularly for intricate parts, can involve hours or days of work. Each stage—wax casting, shell creation, metal pouring—requires precision and deliberate control.
Both in cooling and in finishing, time and care are essential because when you push or force it, that’s when things crack or warp. To maximize your time, prep tools and materials in advance and try to work on batches whenever you can.
Potential for Casting Defects
Issues such as air bubbles, fissures, or uneven texture may occur. The ceramic shell is subject to failure under tension, so thin or intricate areas can shatter. The metal selection is important as well, since each shell does not go with every metal.
Quality checks, such as checking for leaks or employing non-destructive tests, can identify issues before they worsen. If problems do arise, increasing wax thickness or decreasing shell robustness are solutions.
Cost Considerations for Production
Lost wax casting involves a lot more than wax and metal. There’s the added expense of shell-building equipment, wax-deposit removal equipment, and labor. When it comes to shorter runs or custom jobs, you can see how the process aligns.
For large, low-complexity parts, it may not be cost-effective given the price. Minimizing cost may involve re-using molds, selecting less expensive metals, or contracting some processes out to specialty shops.
Mastering Casting Quality Control
Quality control in lost wax casting is crucial to the success of each individual piece. Even a small defect, like a bubble or void in the metal, can drastically compromise a component’s strength. It can indeed cause it to become unusable.
Controlling the process prevents all of these problems. Effective quality control helps to provide a safe work environment. Equipment issues cause the majority of shop-related incidents, so ensuring that equipment is routinely inspected and maintained is critical.
How Material Choices Impact Results
Material choices are everything. We hear it often—there’s a shortage of good quality materials. Using wax that’s either too soft or too hard can destroy the detail of your project.
Most users choose microcrystalline wax for its superior bend and tack. Getting the correct combination of investments and both the wax and the metal together is imperative. This unique combination provides superior resistance against cracking or chipping in the mold.
Safety, handling, and pouring temperature are also key factors. Silver, for example, requires a mold that can withstand the metal’s 1,850°F pour temperature. Choose materials that best complement the mold and the metal to achieve the best, cleanest, and strongest casts.
Temperature Control is Crucial
Temperature control is crucial. Maintaining a consistent temperature and heat is important. Silver may melt at 1,763°F, but it actually requires a few hundred more degrees of heat to really get it to flow.
If the temperature drops or increases unexpectedly, it can result in pockets of gas being trapped or cause a coarse surface to form. Using a kiln that holds a set temperature, plus tools that check the heat in real time, keeps things on track.
In addition, casting quality increases when adequate air vents in the mold allow gas to escape, reducing defects.
Cooling Rates and Metal Structure
The rate at which the cast cools affects the structure of the metal. A decently slow cool increases the size of the metal grains, creating a softer, shinier metal.
Quick cooling increases hardness at the expense of being brittle and can lock in stress. Metal racks or sand beds allow for more controlled cooling, allowing producers to choose the optimal finish.
Advanced Wax Formulations Matter
Advanced wax formulations matter. Improved wax mixes allow for a higher level of detail and less room for error. Waxes that use unique fillers or improved adhesive make for sharper edges and smoother finishes.
Other shops have adopted advanced wax formulations that include materials such as plastic or resin to achieve ultra fine features while reducing waste.
Solving Common Casting Problems
Lost wax casting can present their own challenges, even for the most experienced pair of hands. Errors ultimately manifest themselves as flaws in completed works and simple, speedy solutions are incredibly helpful. Identifying these problems early prevents wasting time and helps ensure a high-quality product.
Remember that every cast is an opportunity to learn, so taking note of the outcome will allow you to make better casts in the future.
Identifying Frequent Casting Defects
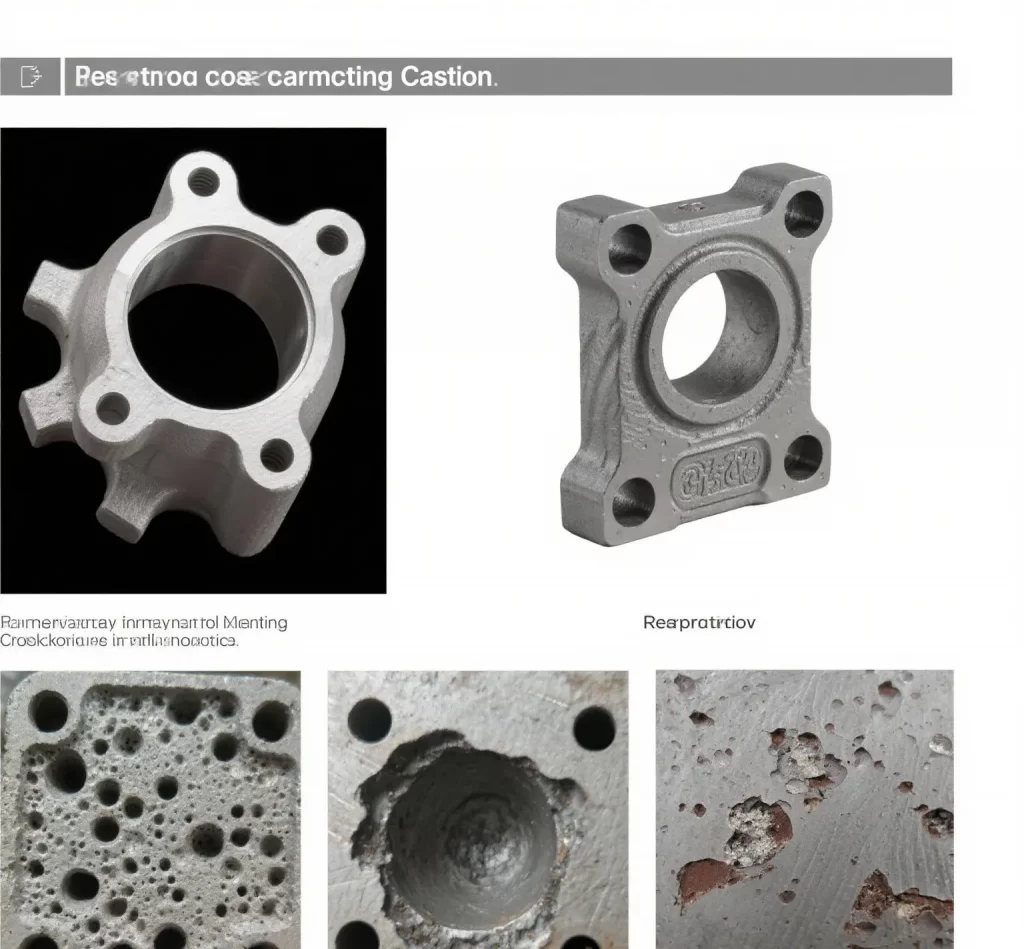
- Common defects and causes:
- Porosity: Low metal temp or trapped gas.
- Shrinkage: Hotspots or poor gating.
- Incomplete fill: Low pouring temp or blocked mold.
- Surface flaws: Dirty wax, poor burnout, or rough molds.
- Visual signs: Small holes, cracks, or unusual structures of cast parts indicate issues, such as porosity or shrinkage. Search out protrusions, pits or metal that is absent at the margins.
- Inspections matter: Diligent inspections at every step identify errors sooner. Inspect under each piece with ample lighting, and don’t hesitate to use a magnifier for finer details.
- Track defects: Write down what you see. Take pictures and make a record of what you did each step of the way. This allows you to identify patterns and correct future casts.
Tips for Minimizing Imperfections
Tips for Minimizing Imperfections include cleaning tools and work areas to prevent blemishes. Degas metal prior to casting, and only introduce borax afterwards.
Trial casting temperatures by increasing them in 50°C (120°F) increments. Use best practices for gating, risers, and mold preparation.
Refer to the guide to identify and troubleshoot hotspots. Sometimes minor adjustments to the process, such as pouring speed or mold venting, can lead to significant improvements.
Troubleshooting Your Process
When troubleshooting problems, change only one variable at a time. Take detailed notes on each batch—what materials you used, temperatures and times.
If you’re getting porosity, experiment with degassing or increasing your casting temperature. Casting shrinkage? Look for rapid-cooling risers or poor gating.
Direct metal solidification to manage the cooling process. With practice, this documentation will assist you in developing and honing your casting.
Safety and Eco-Friendly Practices
Lost wax process casting integrates art and science, yet it carries risks and effects that require savvy management. Safety is what allows everyone to stay healthy in the studio. Sustainable practices not only protect our environment, they protect the future of the craft. Knowing what to wear, how to maintain tools, and how to reduce waste are all important.
Today, makers in the U.S. Around the world are combining time-tested skills with cutting-edge green tools. Together, this powerful combination is helping make casting smarter and safer.
Essential Safety Gear and Rules
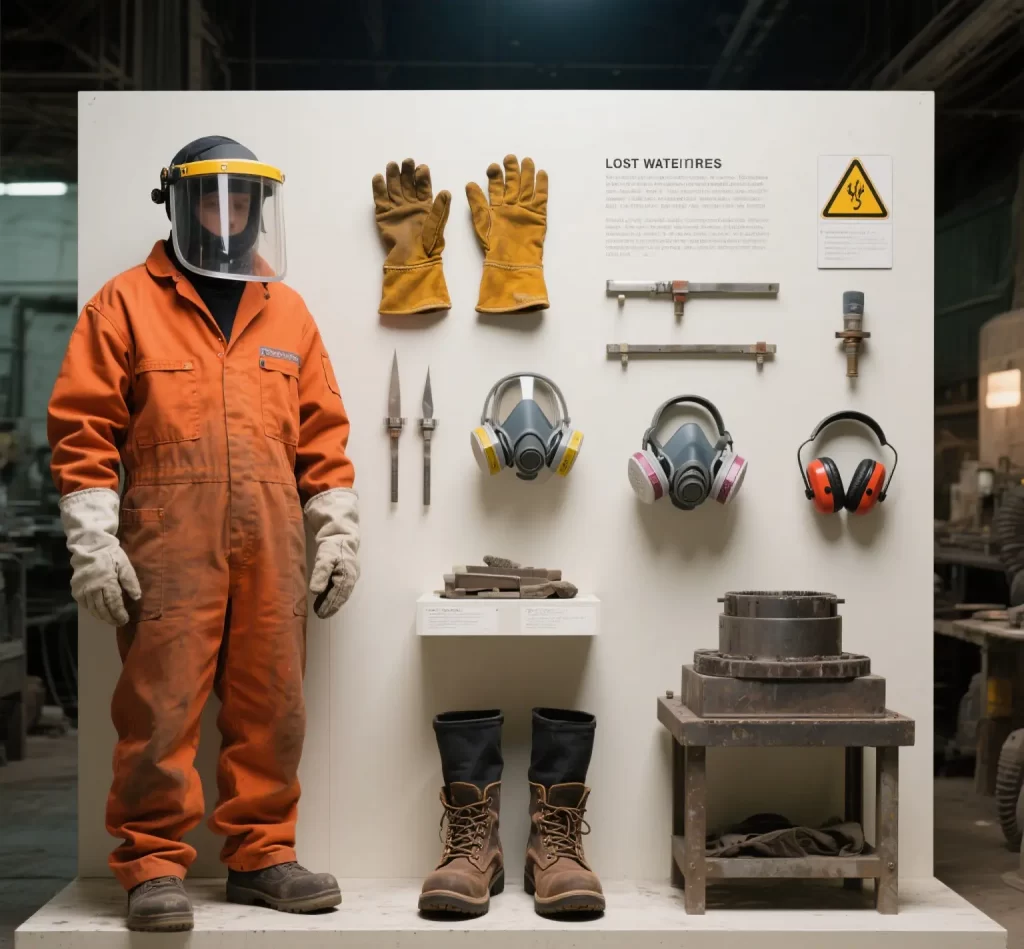
- Heat-resistant gloves
- Face shield or safety goggles
- Fire-resistant apron or clothing
- Closed-toe shoes
- Respirator mask
- Ear protection
During the handling process, wearing this gear at each stage reduces the risk of burns, eye injuries, and lung damage. Studios need steady rules: no food or drink near work, label chemicals, keep exits clear, and know where fire tools are.
Having visible signage, safety meetings and discussions, and buddy system checks create an environment where culture of safety is a priority.
Maintaining Your Casting Equipment
You’ll find that the cleaner your tools, the greater the reduction in risk. Clean machines after use, sweep up any grinded mess, and keep our tools dry and clean. Repair damaged cords or hoses immediately.
Change filters and clean vents for better air quality. When tools are made to last longer, taxpayers save money and waste decreases. Look up manual suggestions and contact professionals for major repairs.
Greener Casting Innovations
Aside from the safety improvements, this innovation in casting greatly reduces harmful emissions. Bio-based or recycled waxes reduce environmental impact. Companies such as HonHo Jewelry in China are leading the industry by using recycled metals and closed-loop water systems.
Eco-friendly alternatives such as these benefit the planet as well as the wallet.
Handling Waste Responsibly
Separate scrap metal to be recycled. Store acids, solvents, and ash in designated containers. Consider using water-saving molds such as drip tape and reusing molds wherever possible.
Educate staff about eco-friendly practices. Locate your local drop-off locations for hazardous materials.
Conclusion
Lost wax casting has an enduring appeal for a reason. Shops in LA and around the country rely on it to create intricate detail and durable metals. Artists, jewelers, and tech people alike are finding new and interesting ways to utilize it. With the right tools and the very best of care, people can achieve some really clean outcomes.
Okay, it involves some patience and a surgeon’s hand, but the work is worth it. Most people can avoid the most frequent slip-ups with simple adjustments and safe practices. It may be a new age of advanced electronics, but sound and tried-and-true tactics still apply. Lost wax process casting keeps it new by combining ancient techniques with modern ingenuity. People who are interested in learning to master the craft of metalworking can register and find out more. Experiment with the process, consult your peers, create what you can.
Frequently Asked Questions
What is the lost wax casting process?
Here’s everything you need to know about the wax casting technique. To begin with, we coat original wax models with a mold material. Finally, we melt the wax out and fill the mold with molten metal to produce intricate jewellery pieces.
What tools do I need for lost wax casting?
You’ll need specialty wax, carving tools, sprues, investment powder, a kiln, a casting flask, and protective gear for the wax casting technique. Most jewelry designers and artists in Los Angeles get these locally.
Can lost wax casting be used for jewelry?
Yes, the wax casting technique can be used for jewelry, and it’s commonly employed in the U.S. due to its ability to create intricate detailing and personalized jewelry pieces. Many local jewelry designers have embraced this method, especially for casting rings and pendants.
How does modern technology improve lost wax casting?
3D printing technology has the potential to make the production of these wax models, integral to the wax casting technique, faster and more precise. This artful marriage of old-world artisanship with new-world technology enhances the jewellery making process and minimizes costly mistakes.
What metals are best for lost wax casting?
Gold, silver, bronze, and brass are the metals you will see most often in jewellery making. All are readily available in the U.S. and cast nicely using the wax casting technique for fine detailed work.
Is lost wax casting eco-friendly?
As long as metals are recycled correctly and waste is disposed of safely, the wax casting technique can be eco-friendly. So no wonder many L.A. jewelry designers are going green.
What are common problems in lost wax casting?
Common problems in the wax casting technique include missing fills, trapped air pockets, and cracking. Quality control checks and a solid jewellery making technique go a long way in preventing these issues.
Dental Industry Innovations
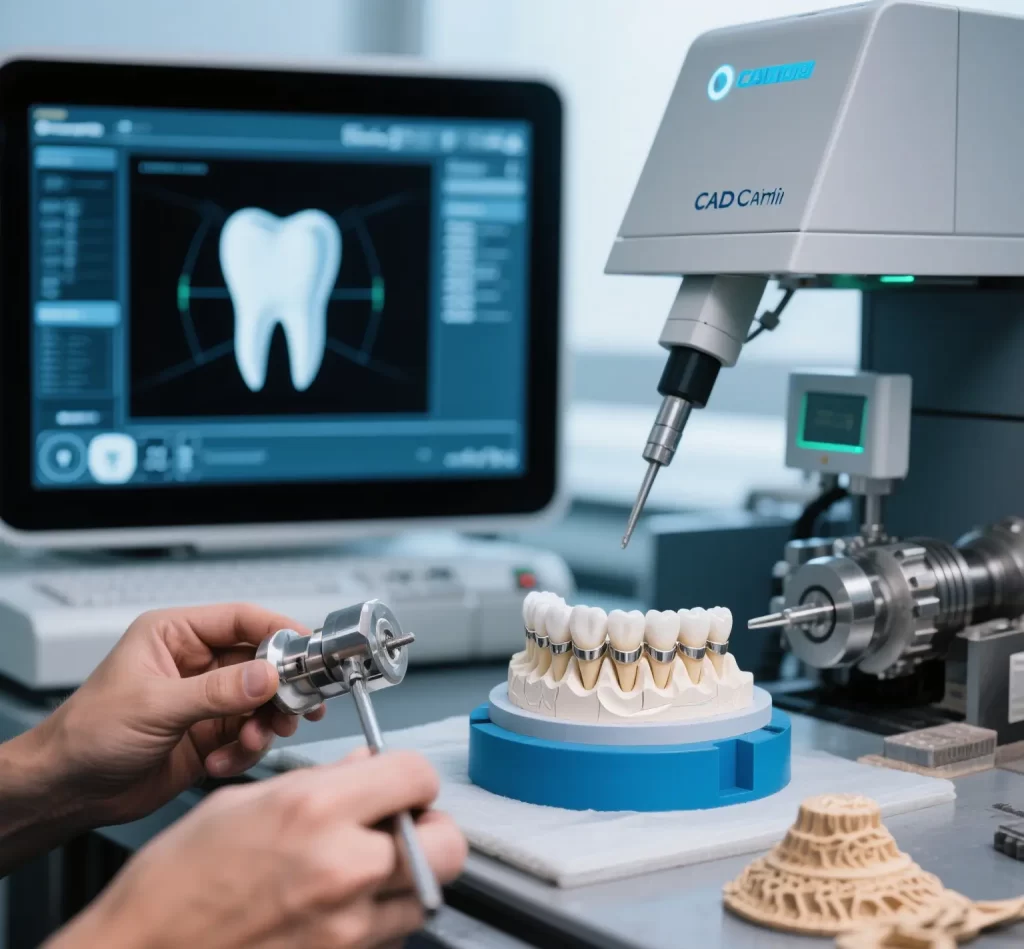
The dental landscape has been radically transformed with improved processes for producing and accommodating dental restoration. Lost-wax casting, or investment casting, has origins that date back thousands of years. Yet, it continues to be an indispensable component of today’s dental industry.
Dentists rely on this process to create custom crowns and bridges fit for any bite with durability designed for a long-lasting smile. The basics are simple: a wax model of the tooth is made, covered with a special investment, and then melted out to leave a mold. This enables dental labs to pour metal only into the areas required.
Major advances occurred during the 19th century when individuals began utilizing uniform casting investments. This resulted in more precise and safer dental procedures. During the latter half of the 20th century, precious alloys were developed exclusively for use in dental applications.
Gold, platinum and other metals provide the strength for crowns and bridges to endure decades of chewing forces. In addition, they continue to be non-invasive and easy on the body. Adding beryllium—2% to 2.5%—increased strength and wear resistance even further.
These metals are capable of handling extreme temperatures between 1700°F and 2000°F. This durability combined with bio-compatibility makes them ideal for demanding applications in the oral environment.
It wasn’t until the end of the 20th century that dentists began adopting CAD/CAM technology. This let them scan teeth and design crowns on a computer, leading to a better fit and less waiting time. Digital design and rapid prototyping, including 3D printing, give dentists the ability to quickly produce complex shapes.
This technology further reduces waste, creating a more efficient process. Ceramic implants and new dental composite materials are changing the face of dental work and providing previously unexpected advantages. They create restorations that last longer and feel more like natural teeth.
Jewelry Production Techniques
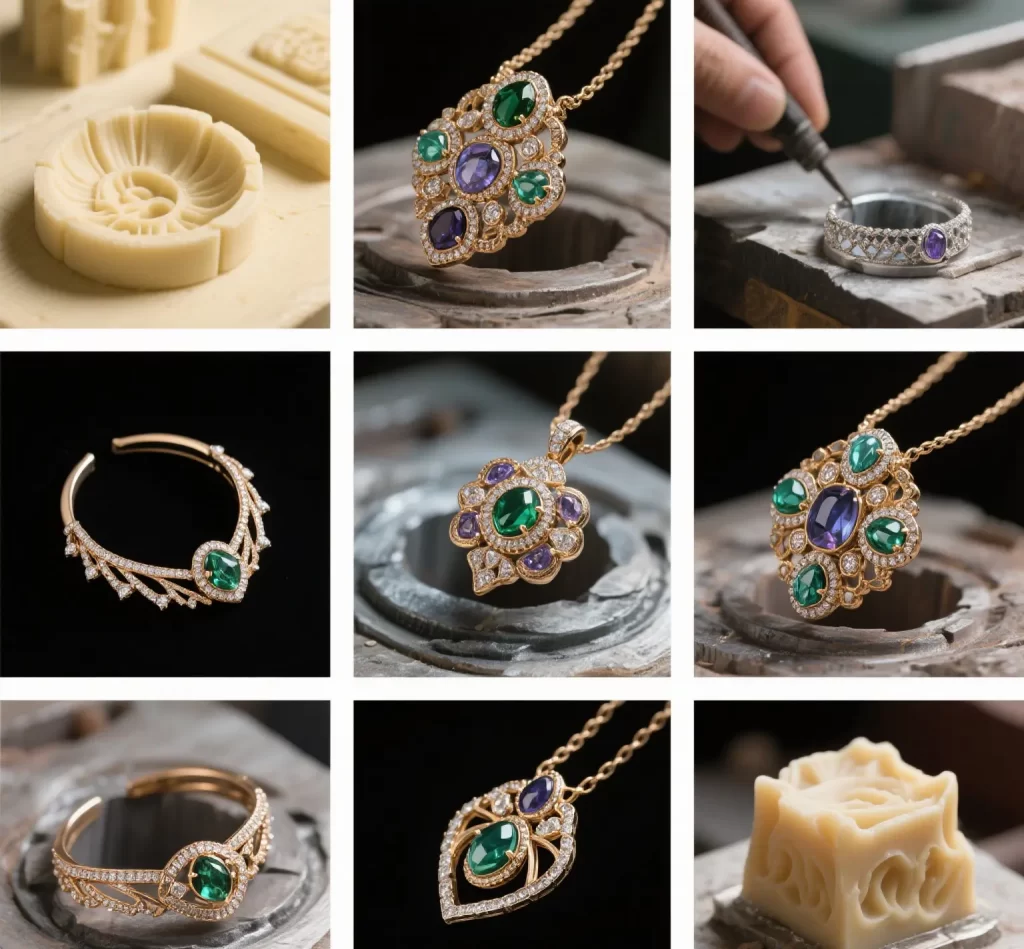
Wax carving is a technique jewelry makers have utilized for more than 6000 years. This ancient technique allows them to achieve delicate lines and intricate details that would be difficult, if not impossible, with other instruments.
The lost wax casting process begins with a wax model, formed to replicate the final piece. This model is then embedded in a mold, and when heat is applied the wax melts away. The void created is filled with a liquid metal, such as silver or gold. The journey through each stage must be thoughtfully crafted.
Wax density is very important here. Wax is very much lighter than metals—in fact about 10 times less heavy than silver and 16 times less heavy than 18-carat gold. To achieve this, makers will frequently make the wax model bigger or thicker than the completed piece. This ensures that the molds end up with the correct shape and weight when it’s cast.
Other waxes There are literally hundreds of wax formulations available for you to choose from. Some wax is hard and nice for sharp edges, and other wax is soft enough that you can bend or press it into shapes. The decision is job dependent.
Burnout is a crucial next stage. This is the stage where the wax is melted out of the mold. Times vary from 2.5 to 12 hours, depending on the size and shape of the project. Complete burnout prevents the creation of defects in the finished metal.
Reducing sprue size is an important step as well. It provides the wax pattern a place to melt out and allows metal to flow in easily. Vacuum casting usually saves the day in this situation. It removes air from the mold and produces a cleaner, crisper cast.
This process only takes approximately 1.5 minutes. After casting, residual pieces or muck are cleaned and pickled off. With a little care and a bit of cleaning you can achieve a beautiful, smooth, bright clean finish.